Design and simulation of an exoesqueleto for the top extremities with 3 degree of freedom and a load of work of 1 kg
Abstract:
This paper presents the design considerations and simulation results for an exoskeleton structure with 3 freedom degrees and 1kg payload. It was designed for rehabilitation processes on people with physical arm disabilities. Four materials were compared, two metallic type: The stainless steel 304 and titanium Ti-6Al-4V (normally used in medicine) and two plastic type, the ABS and nylon 6/6 which are most used in 3D printing process. Height average from anthropometric tables for Ecuador male and female populations where taken into design considerations for the prototype, establishing the maximum sections for the exoskeleton and the forces acting over it. Additionally, the minimum cross section was calculated for each element. Then, analyzed using Gerber theory finding a security factor of two, modifying the fatigue resistance of the elements. Comparing the cross section results and elements strength simulations results for the four materials, was possible to conclude that the two most efficient materials are the titanium Ti-6Al-4V and the nylon 6/6, given their ductile characteristics requiring a lesser cross section on the elements. Finally, the simulation has proven the feasibility of building prototypes for rehabilitation using manufacturing techniques by deposition of material known as 3D printing.
Año de publicación:
2018
Keywords:
- Exoskeleton design
- Mechanical simulation
- Rehabilitation mechanism
- Physical arm disabilities
Fuente:
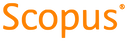
Tipo de documento:
Article
Estado:
Acceso restringido
Áreas de conocimiento:
- Ingeniería mecánica
- Robótica
Áreas temáticas de Dewey:
- Física aplicada
- Otras ramas de la ingeniería

Objetivos de Desarrollo Sostenible:
