Improvement of a knee prosthesis mechanism through experimental stress analysis and the finite element method
Abstract:
In this work, the improvement of a knee mechanism prosthesis is presented. The mechanism is oversized and has an excessive weight to load ratio. The excess weight causes discomfort and an increase in the consumption of metabolic energy of the prosthesis user. To improve the mechanism, a validation of the finite element model of the original device was performed through non-destructive experimental tests. The experimental loads ranged from the weight of a 65-kilogram user to the maximum load of the main structural test of the ISO 10328 standard. Strain gages were installed on the prototype and connected to a system of acquisition, filtering, and amplification of signals, designed, and constructed for this purpose, with which the device strains were measured. Then, the model was simulated with the experimental loads, and the maximum difference found between the experimental and numerical results was 12.43 %; therefore, the model was considered validated. Afterwards, geometric modifications were made to the model and the new simulations to the improved model resulted in a better distribution of the safety factor, a decrease of the safety factors up to 97 % and of the weight up to 43 %, maintaining its structural integrity.
Año de publicación:
2017
Keywords:
- Simulation
- Prosthesis
- EXPERIMENTAL
- Optimization
- Validation
Fuente:
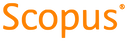
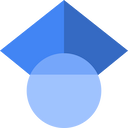
Tipo de documento:
Conference Object
Estado:
Acceso restringido
Áreas de conocimiento:
- Ingeniería mecánica
Áreas temáticas de Dewey:
- Ingeniería y operaciones afines
- Física aplicada
- Otras ramas de la ingeniería

Objetivos de Desarrollo Sostenible:
- ODS 3: Salud y bienestar
- ODS 12: Producción y consumo responsables
- ODS 9: Industria, innovación e infraestructura
