Modeling and implementation of a proportional hydraulic system to control the position and pressure of a plastic extruder
Abstract:
In this research, a proportional hydraulic system for the position control of a double-acting cylinder using Fuzzy Logic and PID for the pressure control of a hydraulic motor is modeled and implemented in a plastic extruder. The closed-loop control system is implemented with Festo's TP 702 Advanced Level Proportional Hydraulics, using a controller, an industrial display, a graphical interface, and a link to MATLAB™ fuzzy control and PID_Tuner for graphics. The modeling provides the process transfer function, proportional control constants, and the position and pressure control graphics, which are then validated between the graphics of the WinCC Advanced interface of the physical process implementation with S7-1200 and 1500 PLCs, generating a graphic comparison of the control of the position and pressure variable. An accuracy error of 1% is generated between the results of the modeling and the physical implementation, which is acceptable in an industrial process. The HMI and the SCADA system have been implemented in WinCC Basic and WinCC Advanced respectively, generating a local and remote real-time graphical interface. The mathematical modeling of the industrial process, its visualization and the real-time information acquisition guarantees the reliability and the optimal behavior of the plastics extrusion process, minimizing the production costs and the raw material waste.
Año de publicación:
2020
Keywords:
- Modeling
- Hydraulic Valves
- MATLAB™
- Position and Pressure Control
- Proportional Control
Fuente:
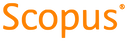
Tipo de documento:
Article
Estado:
Acceso restringido
Áreas de conocimiento:
- Hidráulica
- Ingeniería mecánica
Áreas temáticas de Dewey:
- Física aplicada

Objetivos de Desarrollo Sostenible:
- ODS 9: Industria, innovación e infraestructura
- ODS 12: Producción y consumo responsables
- ODS 8: Trabajo decente y crecimiento económico
