Pillar fracturing production enhancement results for mature, clay sensitive reservoir in Ecuador
Abstract:
This paper discusses pillar fracturing technique application along with customized fluids formulation in a mature oilfield (low reservoir pressure and high permeability) where complex mineralogy limited the use of traditional stimulation practices. Integrated reservoir analysis, laboratory tests (fracturing gel, chemical consolidation resin) and hydraulic fracture modeling performed to obtain a major productivity increase (up to 16x increase) by a combination of tip screen out (TSO) and pillar fracturing techniques. The combination of clay sensitivity, low pressure and high permeability requires a careful planning stage for pillar fracturing (PF) application. The first step is to evaluate PF feasibility by a candidate selection factor using geomechanical parameters such as closure stress, net pressure, etc. The next step is to customize the fracturing gel to sustain high shear stress during TSO and guarantee a complete gel break. Pillar stability is supported by confined stress developed by the surface modification agents mixed on the fly with proppant. This stage requires laboratory tests based on resin hardener ratio at reservoir temperature and time. Clays such as kaolinite, chlorite, etc., limits the applicability of traditional acid stimulation blends on this reservoir. Completion brine as well as fracturing gel requires the addition of a quaternary amine to temporally avoid fines migration during workover operations before and after fracturing. Without this customization, conventional or even pillar fracturing will perform below expectations. Not all reservoirs are candidates for pillar fracturing, candidate selection is a critical step in the planning process. Two types of candidates are documented on this paper, new fracturing as well as re-fracturing jobs. For both cases a numerical gridded fracture simulator is used to understand fracture geometry, diagnose and match previous treatments. Pillar fracturing is designed and executed using pulsed or cycled proppant fracture stimulation, providing infinite acting conductivity for enhanced hydrocarbon production. It significantly reduces screen out tendency leading to higher proppant concentration, as well as total proppant mass reduction when compared to conventional TSO fracture design. The use of surface modification agents (SMA) improves pillar stability and reduces proppant flow back risk if adequate compressive strength is developed during curing time after fracturing operations. Production results show up to 16 times increase, exceeding expected production by conventional fracturing. A complete workflow to characterize, design and simulate a pillar fracturing job using proprietary geomechanical candidate selection criteria is presented. The combination of TSO and pillar fracturing yields a significant production increase over conventional fracturing and acid stimulation. The use of gridded 3D simulator significantly improves the understanding of previous fracturing jobs helping to propose improvements on fracture initiation depth, polymeric load and pumping schedule for re-fracturing candidates.
Año de publicación:
2021
Keywords:
Fuente:
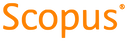
Tipo de documento:
Conference Object
Estado:
Acceso restringido
Áreas de conocimiento:
- Petróleo
Áreas temáticas de Dewey:
- Aceites, grasas, ceras y gases industriales