Combining the STEP-NC standard and forward and inverse kinematics methods for generating manufacturing tool paths for serial and hybrid robots
Abstract:
The different forms of data representation have created the need for a common language capable of describing the design, manufacturing and measurement data. ISO 14649, known as STEP-NC, began as an effort to standardise product data exchange typically for computerised numerical control (CNC). However, although there are several studies involving the application of STEP-NC in CNC machines, which use the G-code format (ISO 6983), there is not much work on the application of STEP-NC in generating programmes for industrial robots, which are being increasingly used in production lines, both in quantity and variety. One of the reasons for the difficulty in applying STEP-NC to robots is that the controller needs to receive commands in a specific language imposed by each manufacturer, resulting in a large number of robot programming languages and difficulty in achieving standardisation. This work proposes a procedure that uses forward and inverse kinematics methods applicable to serial and hybrid robots, allowing STEP-NC-compliant information to be received and generates the path along which the robot should move, reducing the time for setup and integration of robots in manufacturing. These paths were tested on three robots with different morphologies, in a virtual environment, confirming the feasibility of the method.
Año de publicación:
2017
Keywords:
- industrial robots
- tool path generation
- inverse kinematics
- prismatic parts
- STEP-NC
Fuente:
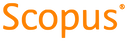
Tipo de documento:
Article
Estado:
Acceso restringido
Áreas de conocimiento:
- Ingeniería de manufactura
- Robótica
Áreas temáticas de Dewey:
- Artes decorativas
- Física aplicada
- Otras ramas de la ingeniería

Objetivos de Desarrollo Sostenible:
- ODS 9: Industria, innovación e infraestructura
- ODS 12: Producción y consumo responsables
- ODS 8: Trabajo decente y crecimiento económico
