Effect of infill parameters on mechanical properties in additive manufacturing
Abstract:
The purpose of this paper is to study and outline the effects of infill parameters (percentage and pattern) using fused deposition manufacturing on mechanical properties of PLA printed samples. Three infill patterns were tested (rectilinear, honeycomb and HilÂbert curve) while infill percentage was tested at three levels (20, 60 and 90 per cent). The properties examined were tensile strength, tensile modulus, elongation, Charpy impact test, morphology of the fractures of tensile and impact test and thermo mechanical analysis. Also, a thermal analysis was done using differential scanÂning calorimetry to the raw polymer in order to determine the proÂcessing temperature. Results showed the influence of the filling parameters in 3D printing on the mechanical properties of the obÂtained part. The filling pattern greatly influences the mechanical properties of parts with low filling percentages. Honeycomb filling pattern is the one with better mechanical results. The complexity of the filling pattern influences on the processing time. Nozzle diÂrection changes in complex patterns lengthening processing time. Results can significantly influence custom design and manufacÂturing of parts using material fused deposition modeling.
Año de publicación:
2020
Keywords:
- Infill percentage
- Pla
- additive manufacturing
- Infill pattern
- Fused deposition modelÂling
Fuente:
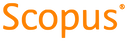
Tipo de documento:
Article
Estado:
Acceso abierto
Áreas de conocimiento:
- Ingeniería mecánica
- Ciencia de materiales
Áreas temáticas de Dewey:
- Metalurgia y productos metálicos primarios

Objetivos de Desarrollo Sostenible:
- ODS 9: Industria, innovación e infraestructura
- ODS 12: Producción y consumo responsables
- ODS 8: Trabajo decente y crecimiento económico
